Stay Cool and Efficient: Industrial Air Conditioning Solutions
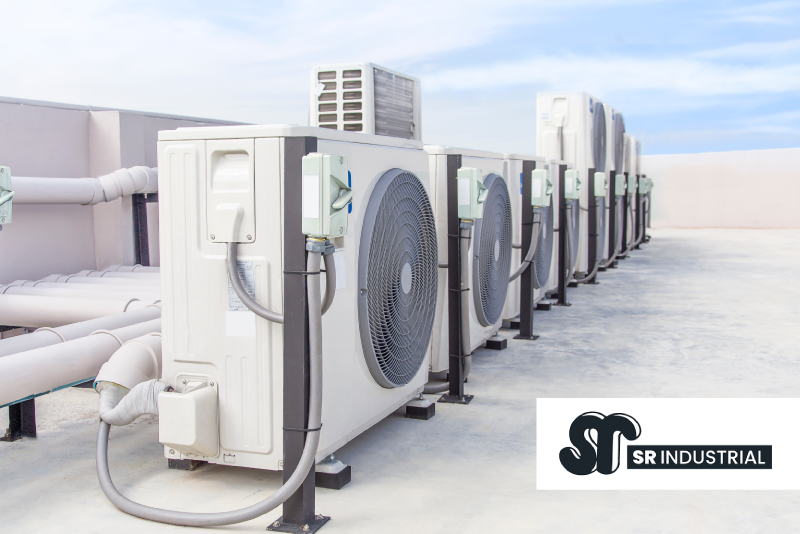
Industrial environments often present unique challenges when it comes to maintaining a comfortable and productive atmosphere. Extreme temperatures, high humidity levels, and air quality concerns can significantly impact both employees and equipment. That’s where industrial air conditioning solutions come into play.
In this article, we will explore the importance of industrial air conditioning and discuss various strategies to stay cool and efficient in these demanding environments.
Understanding Industrial Air Conditioning Systems
Industrial air conditioning differs significantly from its residential counterpart. While residential systems focus on individual comfort, industrial air conditioning systems tackle large-scale cooling requirements. These systems consist of several essential components working together seamlessly.
Compressors: The Heart of the System
The compressor serves as the heart of an industrial air conditioning system. It plays a crucial role in pressurising the refrigerant and maintaining proper circulation. Industrial compressors are designed to handle high loads and ensure efficient cooling across the facility.
Cooling Towers: Managing Heat Dissipation
Cooling towers are responsible for managing the heat dissipated by the air conditioning system. They help remove excess heat by utilising evaporation and convective cooling processes. Proper maintenance and operation of cooling towers are essential for maximising energy efficiency.
Air Handling Units: Distributing Conditioned Air
Air handling units (AHUs) are responsible for distributing conditioned air throughout the industrial facility. These units house filters, fans, and heat exchange coils. AHUs play a critical role in ensuring proper airflow and temperature control in different zones.
Ductwork: Ensuring Efficient Airflow
Efficient ductwork design is crucial to ensure optimal airflow and distribution of conditioned air. Properly sized and insulated ducts help minimise energy loss and maintain consistent temperature levels across the facility.
Controls and Automation: Optimising Performance
Controls and automation systems provide precise monitoring and regulation of industrial air conditioning systems. They help optimise performance, reduce energy consumption, and allow for convenient scheduling and remote management.
Choosing the Right Industrial Air Conditioning Solution
Selecting the appropriate industrial air conditioning solution requires careful consideration of cooling requirements, system types, and energy efficiency considerations.
Assessing Cooling Requirements
Understanding the cooling requirements of your industrial facility is the first step towards choosing the right air conditioning solution. Factors such as heat load calculations, facility size, occupancy levels, and process requirements should be taken into account.
Types of Industrial Air Conditioning Systems
There are different types of industrial air conditioning systems available, each catering to specific needs.
Centralised Systems: Cooling Large Spaces
Centralised systems are ideal for cooling large industrial spaces. They consist of a single central unit that distributes conditioned air through a network of ducts. Centralised systems provide uniform cooling but require significant upfront investment.
Decentralised Systems: Zonal Cooling Solutions
Decentralised systems offer zonal cooling solutions, allowing independent control of temperature in different areas of the facility. These systems are flexible, cost-effective, and are suitable for facilities with varying cooling requirements.
Hybrid Systems: Combining the Best of Both Worlds
Hybrid systems combine the benefits of centralised and decentralised systems. They offer zonal control while utilising a central unit for cooling in common areas. Hybrid systems provide a balance between customisation and energy efficiency.
Energy Efficiency Considerations
Energy efficiency is a critical factor in industrial air conditioning. Implementing energy-efficient components and technologies can lead to significant cost savings and reduced environmental impact.
Variable Speed Drives: Balancing Performance and Energy Savings
Variable speed drives (VSDs) allow the compressor and other components to adjust their speed based on cooling demands. This dynamic control helps optimise energy consumption and maintain desired comfort levels efficiently.
Integrated Controls: Monitoring and Optimisation
Integrated controls and automation systems enable real-time monitoring and optimisation of industrial air conditioning systems. By analysing data and adjusting settings, these systems ensure efficient operation and identify areas for improvement.
Installation and Maintenance Best Practices
Proper installation and regular maintenance are essential for ensuring the longevity and optimal performance of industrial air conditioning systems.
Working with Experienced HVAC Professionals
When it comes to installing an industrial air conditioning system, it’s crucial to work with an experienced HVAC engineer. Assess their expertise, track record, and ensure they have the necessary certifications and licences. A skilled team will understand the unique requirements of your facility and design a customised system that meets your specific needs.
Importance of Regular Maintenance
Regular maintenance plays a vital role in the efficiency and reliability of industrial air conditioning systems.
Scheduled Inspections and Servicing
Periodic inspections and servicing by qualified technicians help identify and address any potential issues before they escalate. These routine checks ensure that all components are functioning optimally, reducing the risk of breakdowns and costly repairs.
Filter Replacements and Cleaning
Clean filters are crucial for maintaining proper airflow and indoor air quality. Regular filter replacements and cleaning prevent clogging and ensure the system operates efficiently, minimising energy consumption.
Calibration and Performance Checks
Calibrating and performing performance checks on the system’s controls and sensors help ensure accurate temperature control and energy efficiency. This ensures that the system operates at its peak performance and minimises energy wastage.
Optimising Industrial Air Conditioning Efficiency
To enhance the efficiency of industrial air conditioning systems, specific strategies can be implemented.
Insulation and Air Sealing Proper insulation and air sealing help prevent energy loss and maintain consistent temperatures within the facility.
Proper Insulation Techniques
Applying insulation to walls, roofs, and floors helps minimise heat transfer between the inside and outside environments. Insulation acts as a barrier, reducing the workload on the air conditioning system and improving overall energy efficiency.
Sealing Air Leaks
Identifying and sealing air leaks in windows, doors, and ductwork prevents conditioned air from escaping and unconditioned air from entering. This not only improves energy efficiency but also enhances comfort levels and indoor air quality.
Airflow Management
Efficient airflow management is crucial for maintaining comfortable and uniform conditions within the industrial facility.
Balancing Air Distribution
Properly balanced air distribution ensures that conditioned air reaches all areas of the facility effectively. Adjusting dampers and airflow control devices helps optimise airflow, preventing hotspots and ensuring consistent cooling throughout the space.
Ventilation Strategies
Implementing effective ventilation strategies ensures the supply of fresh air while maintaining indoor air quality. Properly designed ventilation systems remove pollutants and control humidity levels, creating a healthier and more comfortable working environment.
Utilising Smart Thermostats and Controls
Smart thermostats and controls offer advanced features for optimising industrial air conditioning systems.
Benefits of Smart HVAC Controls
Smart controls provide precise temperature management, scheduling capabilities, and remote monitoring. They allow facility managers to fine-tune settings and make real-time adjustments, maximising energy efficiency without compromising comfort.
Automation and Scheduling for Efficiency
Automation features enable the system to operate based on pre-set schedules and occupancy patterns. By minimising unnecessary cooling during unoccupied periods, energy consumption is reduced, leading to cost savings.
Special Considerations for Specific Industries
Different industries have unique requirements when it comes to industrial air conditioning.
Food Processing and Cold Storage Facilities
In food processing and cold storage facilities, maintaining optimal temperature and humidity levels is crucial for preserving product quality and safety.
Maintaining Optimal Temperature and Humidity Levels
Industrial air conditioning systems in these facilities must be capable of precise temperature and humidity control to ensure food freshness and prevent spoilage. Specialised refrigeration systems and humidity control equipment are often required.
Controlling Airborne Contaminants
Airborne contaminants, such as bacteria and allergens, can pose a risk in certain industrial environments such as food processing facilities. Implementing air filtration systems and proper ventilation techniques helps control and minimise the presence of contaminants, ensuring a safe and hygienic working environment.
Data Centres and Server Rooms
Data centres and server rooms house sensitive equipment that generates a significant amount of heat. Maintaining optimal temperature and humidity levels is crucial for equipment performance and longevity.
Precision Cooling for Sensitive Equipment
Industrial air conditioning systems in data centres and server rooms utilise precision cooling solutions to maintain stable temperatures around critical equipment. These systems employ specialised cooling techniques such as precision air conditioning units and in-row cooling to ensure consistent and targeted cooling.
Redundancy and Backup Systems
To prevent downtime and equipment failure, redundant cooling systems and backup power solutions are essential in data centres. These systems provide fail-safe measures to ensure uninterrupted operation even in the event of equipment failure or power outages.
Manufacturing and Industrial Processes
Industrial processes, such as manufacturing, often generate high levels of heat and require specialised air conditioning solutions to maintain a productive environment.
Process Cooling and Temperature Control
In manufacturing facilities, air conditioning systems play a vital role in process cooling and temperature control. Cooling equipment and systems are designed to handle specific heat loads and maintain precise temperatures required for efficient manufacturing processes.
Minimising Downtime and Equipment Failure
Effective industrial air conditioning systems help minimise downtime and equipment failure by preventing overheating and maintaining stable operating conditions. Regular maintenance and monitoring are crucial to identify and address any issues before they impact production.