Clean Room Construction: Designing and Building Controlled Environments
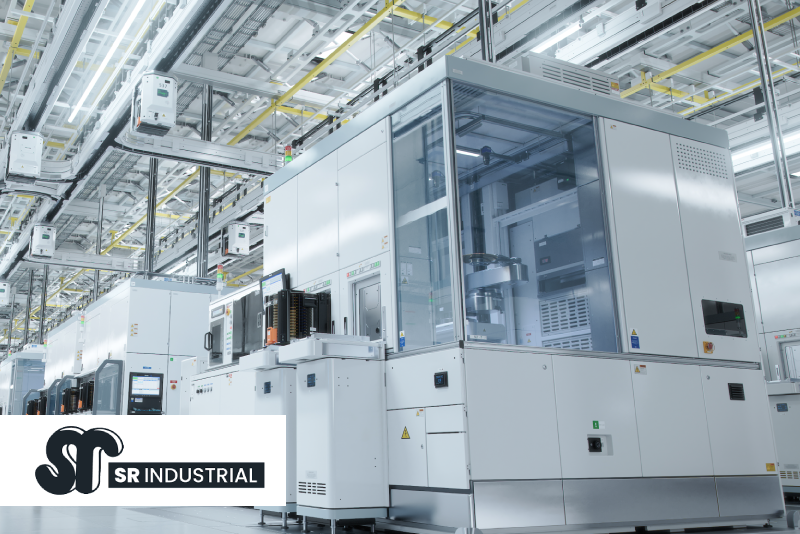
Introduction
Clean room construction plays a critical role in industries where the control of airborne contaminants is paramount. From pharmaceutical manufacturing to semiconductor production, clean rooms provide a controlled environment to ensure product quality, safety, and compliance with stringent regulations.
In this article, we will delve into the intricacies of clean room construction, exploring the design considerations, construction process, challenges, cost analysis, and future trends. Join us as we uncover the key elements that make clean room construction a vital aspect of modern industries.
Design Considerations for Clean Rooms
Defining Clean Room Classification
To create an effective clean room, it is essential to understand the concept of clean room classification. The International Organisation for Standardisation (ISO) provides guidelines for clean room classification, which are commonly used across industries. These classifications are based on particle count and define the maximum allowable concentration of particles per cubic meter of air.
ISO Standards for Clean Room Classification
ISO standards, such as ISO 14644-1 and ISO 14644-2, provide specific guidelines for particle count and clean room classes. These standards categorise clean rooms into different classes, ranging from ISO Class 1 (the cleanest) to ISO Class 9 (the least clean). Understanding the clean room class requirements is crucial for designing and constructing a clean room that meets the desired cleanliness level.
Determining the Required Clean Room Class
When embarking on a clean room construction project, it is crucial to determine the required clean room class based on the specific industry and application. Factors such as product sensitivity, manufacturing processes, and regulatory requirements will influence the clean room class selection. Working closely with clean room consultants and industry experts will help ensure accurate determination of the required class.
Factors Influencing Clean Room Design
Airborne Contaminants and Filtration
Controlling airborne contaminants is fundamental to clean room design. High-efficiency particulate air (HEPA) filters are widely used to remove particles from the air, ensuring the desired cleanliness level is achieved. Factors such as filter efficiency, air change rates, and filter maintenance play a crucial role in maintaining clean air within the clean room.
Temperature and Humidity Control
Maintaining appropriate temperature and humidity levels is essential to prevent condensation and microbial growth within the clean room. The HVAC (heating, ventilation, and air conditioning) system must be designed to regulate temperature and humidity effectively, ensuring optimal conditions for both products and personnel.
Airflow Patterns and Direction
The direction and flow of air within a clean room have a significant impact on contamination control. Properly designed airflow patterns, such as laminar flow or turbulent flow, help prevent the build-up of contaminants and ensure their removal from critical areas. Balancing air supply and exhaust is vital to maintain pressure differentials that prevent unfiltered air from entering the clean room.
Material Selection and Surface Finishes
Selecting appropriate materials and surface finishes is crucial to minimise contamination risks and facilitate cleaning and disinfection. Non-porous, smooth, and easy-to-clean surfaces are preferred, and materials with low particle shedding and chemical resistance are commonly used in clean room construction.
Clean Room Layout and Segregation
Efficient clean room layout design involves proper segregation of different clean room areas, such as gowning rooms, production areas, and equipment storage. The flow of personnel, materials, and equipment should be carefully considered to minimise cross-contamination risks and ensure smooth operations.
Lighting and Electrostatic Discharge (ESD) Control
Lighting in clean rooms should provide adequate illumination while minimising the introduction of contaminants. Special attention is given to ESD control, as electrostatic discharge can damage sensitive products or disrupt electronic components. Proper grounding and the use of anti-static materials are essential to mitigate the risk of ESD within the clean room environment.
Clean Room Construction Process
Pre-Construction Phase
Before breaking ground on a clean room construction project, thorough planning and preparation are crucial. The pre-construction phase involves several key steps to ensure a successful project.
Establishing Project Requirements and Goals
Clear identification of project requirements and goals is essential to set the foundation for clean room construction. Understanding the specific needs of the industry, regulatory compliance, and desired cleanliness level will guide the entire construction process.
Budgeting and Cost Estimation
Accurate budgeting and cost estimation are essential for successful clean room construction. It involves evaluating the costs of materials, equipment, labour, permits, and ongoing maintenance. Collaborating with experienced clean room construction professionals will help create a realistic budget and avoid cost overruns.
Regulatory Compliance and Permits
Complying with regulatory requirements is a critical aspect of clean room construction. Different industries have specific regulations and standards, such as those set by the FDA for pharmaceutical clean rooms. Obtaining the necessary permits and ensuring compliance with building codes are vital to avoid legal issues and ensure the clean room meets all necessary standards.
Design and Planning Phase
The design and planning phase is a crucial step in clean room construction, where the foundation for a well-designed and functional clean room is laid.
Engaging Architects and Clean Room Consultants
Collaborating with architects and clean room consultants is vital to translate project requirements into a comprehensive clean room design. Their expertise ensures that the clean room layout, airflow, materials, and systems align with industry standards and best practices.
Clean Room Design Specifications
During this phase, detailed clean room design specifications are created. This includes floor plans, equipment placement, HVAC system design, lighting, and electrical system requirements. Each element must be carefully considered and integrated into the overall design to optimise cleanliness, functionality, and safety.
Construction Timeline and Scheduling
Creating a realistic construction timeline and schedule is essential for project management. This includes defining milestones, setting deadlines, and coordinating with subcontractors, suppliers, and construction teams. Effective project management ensures that the construction process remains on track and meets the desired completion date.
Material Procurement and Vendor Selection
Procuring high-quality materials and selecting reliable vendors is crucial for clean room construction. Working with reputable suppliers who understand the specific requirements of clean room environments helps ensure the availability of suitable materials and timely delivery.
Construction Phase
The construction phase brings the clean room design to life, transforming plans into a fully functional clean room environment.
Site Preparation and Safety Measures
Preparing the construction site and implementing appropriate safety measures are the first steps in the construction phase. This includes ensuring proper ventilation, dust control, and personal protective equipment (PPE) for construction workers to prevent contamination of the clean room area.
Clean Room Components and Installation
Installing clean room components requires attention to detail and precision. Key components include walls, ceilings, and floors designed to meet cleanliness requirements and provide proper insulation. HVAC systems and air handling units are carefully integrated to ensure effective temperature, humidity, and particle control. Filtration systems with HEPA filters are installed to remove contaminants from the air, while lighting and electrical systems are positioned to avoid interference with cleanliness or ESD concerns. Entryways and airlocks are constructed to maintain pressure differentials and limit particle ingress. Finally, suitable furniture and fixtures are chosen to support clean room activities.
Testing, Commissioning, and Validation
Thorough testing, commissioning, and validation procedures are essential to verify that the clean room meets the desired cleanliness level and functional requirements. This involves conducting air particle count tests, airflow measurements, and verifying the performance of HVAC systems, filtration systems, and other critical components. Once the clean room passes the necessary tests, it can proceed to the next phase.
Post-Construction Phase
The post-construction phase focuses on finalising the clean room project and ensuring its ongoing maintenance and compliance.
Clean Room Certification
Obtaining clean room certification is a crucial step to validate the cleanliness and functionality of the constructed clean room. Certification is typically performed by independent third-party organisations or clean room consultants who conduct thorough inspections and tests to ensure compliance with industry standards and regulatory requirements.
Training and Documentation
Proper training and documentation play a vital role in maintaining the clean room’s integrity and ensuring the ongoing compliance of personnel. Training programs should cover topics such as gowning procedures, clean room protocols, contamination control, and emergency response. Additionally, comprehensive documentation should be maintained, including standard operating procedures (SOPs), maintenance schedules, and validation reports.
Ongoing Maintenance and Upkeep
Regular maintenance and upkeep are necessary to sustain the cleanliness and functionality of the clean room. This includes routine cleaning, filter replacement, HVAC system maintenance, and periodic inspections to identify and address any potential issues. Adhering to maintenance schedules and implementing proper cleaning protocols is essential for long-term success.
Clean Room Construction Challenges and Solutions
Despite the benefits of clean room construction, there are inherent challenges that must be addressed to ensure successful project outcomes.
Controlling Contamination during Construction
During the construction phase, preventing contamination from construction activities is crucial. Implementing stringent construction site management practices, including dust control measures, clean construction practices, and proper waste management, helps minimise contamination risks. Construction materials with low particle shedding properties should be selected, and construction personnel should be educated on clean room protocols to maintain cleanliness throughout the process.
HVAC System Design and Performance
The design and performance of the HVAC system are critical to maintaining the desired clean room conditions. Balancing airflow, pressure differentials, and temperature and humidity control is essential. Regular maintenance and filter replacement are necessary to ensure the optimal performance of the HVAC system and prevent contamination due to system malfunction.
Integration of Clean Room Equipment and Services
Integrating process equipment, utilities, and services within the clean room environment requires careful planning and coordination. Equipment should be properly installed, positioned, and connected to avoid interfering with cleanliness requirements. Waste handling and disposal methods must comply with regulatory guidelines to prevent contamination and maintain the integrity of the clean room environment.
Adherence to Regulatory Standards and Guidelines
Different industries have specific regulatory standards and guidelines that govern clean room construction. For example, pharmaceutical clean rooms must comply with strict FDA regulations to ensure product quality and patient safety. Adherence to these standards is essential to avoid regulatory penalties and maintain compliance.
Clean Room Construction Cost and ROI Analysis
Factors Influencing Clean Room Construction Costs
Several factors impact the cost of clean room construction. Clean room class and size, design complexity and customisation, construction materials and finishes, HVAC and filtration systems, and the inclusion of specialised equipment and utilities all contribute to the overall cost. Proper budgeting and cost estimation during the planning phase are crucial to avoid cost overruns.
Return on Investment (ROI) Considerations
While clean room construction can be a significant investment, it offers several tangible benefits that contribute to the ROI. Operational efficiency and productivity are enhanced by reducing contamination risks and maintaining product integrity. Compliance with regulatory standards safeguards against costly regulatory penalties. Additionally, a clean room environment ensures enhanced product quality and safety, fostering customer satisfaction and market reputation.
Future Trends in Clean Room Construction
Clean Room Automation and Industry 4.0
Clean room construction is witnessing the integration of automation technologies and the emergence of Industry 4.0 principles. Automation plays a vital role in enhancing operational efficiency, reducing human error, and improving process control within clean room environments. Automated systems for monitoring and controlling critical parameters such as temperature, humidity, and airflow enable real-time adjustments and proactive maintenance, ensuring optimal performance and adherence to cleanliness standards.
Modular Clean Room Solutions
Modular clean room solutions are gaining popularity due to their flexibility and cost-effectiveness. These pre-engineered clean room modules can be easily assembled, disassembled, and reconfigured as per changing requirements. They offer scalability, quick installation, and the ability to adapt to different clean room classes and sizes. Modular clean rooms are particularly suitable for industries that require frequent reconfiguration or have limited space availability.
Sustainable and Energy-Efficient Designs
Sustainability and energy efficiency are becoming significant considerations in clean room construction. Energy-efficient HVAC systems, LED lighting, and advanced control systems help reduce energy consumption and minimise environmental impact. The use of eco-friendly construction materials and implementing waste reduction and recycling practices contribute to sustainable clean room operations.
Advancements in Clean Room Materials and Technologies
Research and development in clean room materials and technologies continue to drive advancements in clean room construction. Innovative materials with improved cleanliness, durability, and chemical resistance properties are being developed. Cutting-edge technologies such as nanofabrication, advanced filtration systems, and contamination monitoring systems are revolutionising clean room capabilities and raising the bar for cleanliness standards.
Conclusion
Clean room construction is a complex and critical process that demands meticulous planning, adherence to standards, and expertise in contamination control. By considering factors such as clean room classification, design considerations, construction processes, challenges, costs, and future trends, industries can achieve highly controlled environments that ensure product quality, regulatory compliance, and customer satisfaction.
As clean room construction continues to evolve, embracing automation, modular solutions, sustainability, and technological advancements will pave the way for cleaner, more efficient, and adaptable clean room environments. With a strong focus on maintaining cleanliness, adhering to regulations, and embracing innovation, clean room construction remains a cornerstone of industries where precision and control are paramount.