Installing An Effective Industrial Heating System
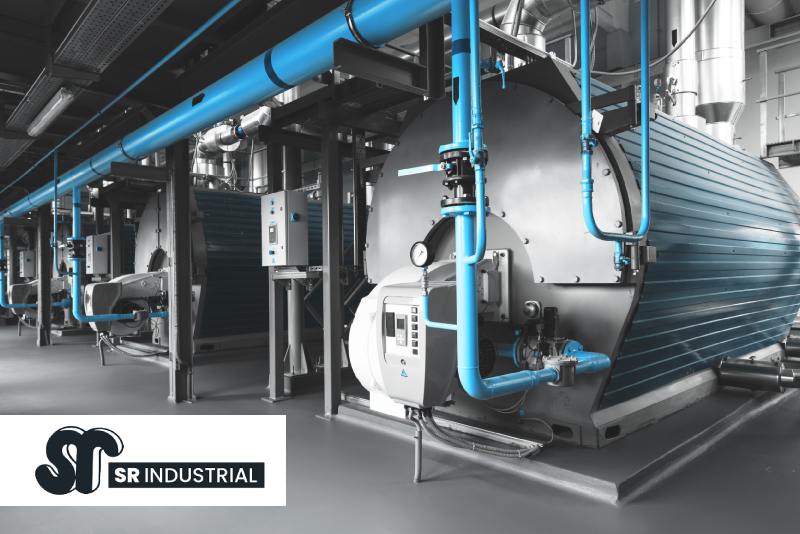
Industrial heating plays a vital role in various manufacturing and processing industries. It is the process of raising the temperature of an object or material using a heat source. Industrial heating is used for a variety of applications, such as melting, drying, smelting, and heat treatment.
In this article, we will explore the different types of industrial heating technologies, their advantages and disadvantages, and their applications.
Types of Industrial Heating
There are three main types of industrial heating: convection heating, radiation heating, and conduction heating.
Convection Heating
Convection heating is a type of industrial heating that uses a fluid, such as air or water, to transfer heat. This works by circulating hot fluid around the object or material to be heated.
The hot fluid transfers its heat to the object, which then raises its temperature.
Radiation Heating
Radiation heating is a type of industrial heating that uses electromagnetic radiation to transfer heat. It works by emitting electromagnetic waves from a heat source, such as a lamp or a furnace, to the object or material to be heated. The electromagnetic waves transfer their heat to the object, which then raises its temperature.
Conduction Heating
Conduction heating is a type of industrial heating that uses direct contact between the heat source and the object or material to transfer heat. It works by placing the object or material in contact with a heat source, such as a hot plate or a furnace. The heat source transfers its heat directly to the object, which then raises its temperature.
Common Heating Technologies Used in Industry
Electric Heating
Electric heating is a heating technology that uses electricity to generate heat. These systems are commonly used in industry due to their efficiency, precision, and controllability. There are several types of electric heating, including resistance heating, induction heating, and dielectric heating.
Types of Electric Heating
- Resistance Heating: Resistance heating is a type of electric heating that uses resistance wires to generate heat. The resistance wires are heated by an electric current, which causes them to produce heat. Resistance heating is commonly used in heating applications that require high temperatures, such as heat treatment and welding.
- Induction Heating: Induction heating is a type of electric heating that uses electromagnetic induction to generate heat. Induction heating works by inducing electrical currents in a conductive material, such as metal, which then produces heat. Induction heating is commonly used in heating applications that require high temperatures and precise control, such as brazing and soldering.
- Dielectric Heating: Dielectric heating is a type of electric heating that uses high-frequency electromagnetic waves to generate heat. Dielectric heating works by subjecting a material to an alternating electric field, which causes the molecules to rotate and produce heat. Dielectric heating is commonly used in heating applications that require uniform heating and drying, such as drying coatings and textiles.
Advantages and Disadvantages of Electric Heating
Electric heating has several advantages and disadvantages, including:
Advantages
- Energy Efficient: Electric heating is energy-efficient compared to other heating technologies, such as gas heating.
- Precise Control: Electric heating allows for precise temperature control, which is essential for heating applications that require precise temperature control.
- Clean: Electric heating is clean and does not produce emissions, which makes it ideal for applications where emissions are a concern.
Disadvantages
- High Initial Cost: Electric heating systems have a high initial cost compared to other heating technologies.
- Limited Capacity: Electric heating systems have a limited capacity compared to other heating technologies.
- Dependence on Electricity: Electric heating systems are dependent on electricity, which can be a concern during power outages.
Gas Heating
This form is a heating technology that uses gas, such as natural gas or propane, to generate heat. Gas heating systems are commonly used in industry due to their high capacity and low operating cost.
Types of Gas Heating
There are two main types of gas heating: direct-fired heating and indirect-fired heating.
- Direct-Fired Heating: Direct-fired heating is a type of gas heating that uses a burner to directly heat the material or object to be heated. Direct-fired heating is commonly used in applications that require high heat output, such as metalworking and glassmaking.
- Indirect-Fired Heating: Indirect-fired heating is a type of gas heating that uses a heat exchanger to transfer heat to the material or object to be heated. Indirect-fired heating is commonly used in applications that require precise temperature control and low emissions, such as food processing and pharmaceutical manufacturing.
Advantages and Disadvantages of Gas Heating
Gas heating has several advantages and disadvantages, including:
Advantages
- High Capacity: Gas heating systems have a high capacity compared to other heating technologies, which makes them ideal for applications that require high heat output.
- Low Operating Cost: Gas heating systems have a low operating cost compared to other heating technologies, such as electric heating.
- Dependable: Gas heating systems are dependable and can operate during power outages, which makes them ideal for applications where reliability is a concern.
Disadvantages
- Safety Concerns: Gas heating systems can be dangerous if not installed and maintained properly. Gas leaks can cause fires or explosions, which can be catastrophic.
- Environmental Impact: Gas heating systems produce emissions, such as carbon monoxide and nitrogen oxides, which can contribute to air pollution and climate change.
- Limited Control: Gas heating systems have limited control over the heat output, which can be a concern for applications that require precise temperature control.
Biomass Heating
Biomass heating is a heating technology that uses biomass, such as wood chips, pellets, or agricultural waste, to generate heat. These heating systems are renewable and sustainable, which makes them ideal for applications where sustainability is a concern. Biomass heating systems are commonly used in heating applications that require low to medium heat output, such as space heating and water heating.
Advantages and Disadvantages of Biomass Heating
Biomass heating has several advantages and disadvantages, including:
Advantages
- Renewable: Biomass heating is renewable and sustainable, which makes it ideal for applications where sustainability is a concern.
- Low Cost: Biomass heating systems have a low operating cost compared to other heating technologies, such as gas heating and electric heating.
- Carbon Neutral: Biomass heating systems are carbon-neutral, which means they do not contribute to greenhouse gas emissions.
Disadvantages
- Limited Capacity: Biomass heating systems have a limited capacity compared to other heating technologies, which makes them unsuitable for applications that require high heat output.
- Fuel Storage: Biomass heating systems require a large storage space for the fuel, which can be a concern for applications with limited space.
- Maintenance: Biomass heating systems require regular maintenance, such as cleaning and fuel management, which can be time-consuming and expensive.
Applications of Industrial Heating
Heat Treatment
This is a process that alters the properties of a material, such as its strength, toughness, and hardness, through heating and cooling. Heat treatment is used in a wide range of applications, such as manufacturing and construction.
Types of Heat Treatment
- Annealing: Annealing is a heat treatment process that involves heating a material to a specific temperature and holding it at that temperature for a specific period, followed by slow cooling. Annealing is used to soften a material, improve its ductility, and relieve internal stresses.
- Normalising: Normalising is a heat treatment process that involves heating a material to a specific temperature, holding it at that temperature for a specific period, and then allowing it to cool in still air. Normalising is used to refine the grain structure of a material, improve its mechanical properties, and relieve internal stresses.
- Quenching: Quenching is a heat treatment process that involves heating a material to a specific temperature and then rapidly cooling it in a liquid, such as water or oil. Quenching is used to harden a material, improve its wear resistance, and increase its strength.
- Tempering: Tempering is a heat treatment process that involves heating a material that has been quenched to a specific temperature and holding it at that temperature for a specific period, followed by cooling in still air. Tempering is used to reduce the hardness of a material, improve its toughness, and relieve internal stresses.
Applications of Heat Treatment in Industry
Heat treatment is used in a wide range of applications in industry. Some of the common applications include:
- Manufacturing: Heat treatment is used in manufacturing applications, such as metalworking and glassmaking, to improve the properties of the material.
- Construction: Heat treatment is used in construction applications, such as concrete curing, to improve the strength and durability of the material.
- Aerospace: Heat treatment is used in aerospace applications, such as aircraft parts, to improve the performance and reliability of the material.
Drying and Curing
- Drying: Drying is a process that involves removing moisture from a material, such as paper, textiles, and coatings. Drying is typically achieved by exposing the material to hot air or gas.
- Curing: Curing is a process that involves a chemical reaction that hardens and strengthens a material, such as adhesives, coatings, and inks. Curing is typically achieved by exposing the material to heat or UV light.
Applications of Drying and Curing in Industry
Drying and curing are used in a wide range of applications in industry. Some of the common applications include:
- Printing: Drying and curing are used in printing applications, such as ink drying and UV curing, to ensure the quality and durability of the final product.
- Coatings: Drying and curing are used in coatings applications, such as paint drying and powder coating, to ensure the adhesion and durability of the coating.
- Adhesives: Drying and curing are used in adhesive applications, such as glue drying and heat curing, to ensure the strength and durability of the bond.
Melting and Smelting
- Melting: Melting is a process that involves heating a material to its melting point and changing its state from solid to liquid.
- Smelting: Smelting is a process that involves melting a material and then extracting a metal or other valuable substance from the molten material.
Applications of Melting and Smelting in Industry
Melting and smelting are used in a wide range of applications in industry. Some of the common applications include:
- Metalworking: Melting and smelting are used in metalworking applications, such as steelmaking and aluminium production, to produce metals and alloys.
- Glassmaking: Melting and smelting are used in glassmaking applications to produce glass products, such as bottles, jars, and windows.
- Ceramics: Melting and smelting are used in ceramic applications, such as pottery and tiles, to produce ceramic products.
Factors to Consider When Choosing an Industrial Heating System
When choosing an industrial heating system, there are several factors to consider. These factors include:
- Cost: The cost of an industrial heating system is an important factor to consider. The initial cost of the system, as well as the operating cost, should be taken into account when choosing a system.
- Efficiency: The efficiency of an industrial heating system is an important factor to consider. Choosing an efficient system will reduce operating costs and improve performance.
- Maintenance: The maintenance needs of an industrial heating system should be considered when choosing a system. Regular maintenance and inspections are necessary to ensure the system is operating safely and efficiently.
- Environmental Impact: The environmental impact of an industrial heating system should be considered when choosing a system. Choosing a system with low emissions will reduce the environmental impact and improve air quality.
- Capacity: The capacity of an industrial heating system should match the heating requirements of the application. Choosing a system with inadequate capacity will result in inefficient heating and increased operating cost.