Industrial Boilers: Powering Efficiency in Large-Scale Operations
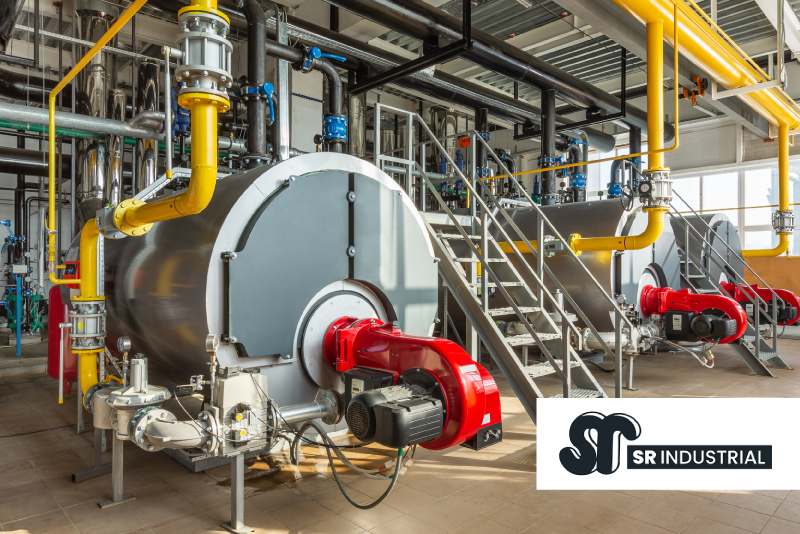
Introduction to Industrial Boilers
Industrial boilers play a crucial role in powering a wide range of industries, providing essential heat and steam for various processes. These robust and efficient machines are designed to generate high-pressure steam by burning fuels, such as natural gas, coal, oil, or biomass, in a controlled combustion process. In this article, we will explore the fascinating world of industrial boilers, their types, key components, selection factors, installation, maintenance, safety considerations, optimisation techniques, troubleshooting, and emerging trends.
Let’s delve into the heart of industrial boiler technology and discover how it continues to drive innovation and productivity across industries.
Types of Industrial Boilers
Fire-Tube Boilers
Fire-tube boilers are one of the most common types used in industrial applications. They consist of a large cylindrical shell filled with water and a series of tubes that run through the boiler’s interior. Hot gases produced by the combustion process pass through these tubes, heating the water and generating steam. Fire-tube boilers are known for their simplicity, compact design, and suitability for low to medium steam demands. However, they have limited capacity and can be slower in producing steam compared to other types.
Water-Tube Boilers
Water-tube boilers operate on a different principle compared to fire-tube boilers. In this design, water is circulated within the tubes while hot gases flow over the exterior, transferring heat to the water. Water-tube boilers are highly efficient, offer faster steam production, and are capable of handling high-pressure applications. They are commonly used in power plants, refineries, and large industrial processes that demand significant steam capacity.
Electric Boilers
Electric boilers are gaining popularity due to their clean and efficient operation. They use electricity as the primary source of heat generation, eliminating the need for fuel combustion. Electric boilers are compact, easy to install, and have precise temperature control capabilities. They are ideal for applications that require quick start-up times, precise temperature control, and where emissions reduction is a priority.
Key Components of Industrial Boilers
Boiler Shell
The boiler shell is the outer structure that encloses the boiler’s internal components. It provides structural integrity, insulation, and protection against external elements. The materials used for the boiler shell are selected based on factors such as operating pressure, temperature, and corrosive environments.
Burners
Burners are responsible for the combustion process by mixing fuel and air in the correct proportions. They play a crucial role in achieving efficient combustion, ensuring complete fuel burnout, and minimising emissions. Burners can use various technologies, such as natural gas, oil, or dual-fuel burners, each offering different advantages and characteristics.
Heat Exchangers
Heat exchangers facilitate the transfer of heat from the combustion gases to the water or steam. They maximise energy efficiency by ensuring optimal heat transfer while minimising heat loss. Heat exchangers can be of different types, including shell and tube, plate, or spiral designs, each suitable for specific applications.
Control Systems
Control systems are the brains behind industrial boilers, regulating and monitoring various parameters, including fuel supply, combustion air, temperature, pressure, and water level. Advanced control systems enhance safety, efficiency, and performance by ensuring precise control and continuous monitoring of critical boiler parameters.
Fuel Delivery Systems
Fuel delivery systems transport the selected fuel to the burners, ensuring a consistent and efficient supply. These systems include fuel storage tanks, pumps, filters, and control valves. Proper fuel delivery systems are essential for reliable and uninterrupted boiler operation.
Factors to Consider When Choosing Industrial Boilers
Boiler Size and Capacity
Selecting the right boiler size and capacity is essential to meet the specific requirements of your industrial process. Factors such as the amount of steam or heat needed, peak load demands, and future expansion plans should be taken into account. Undersized boilers may struggle to meet the demand, leading to inefficiencies and reduced performance, while oversized boilers can result in unnecessary energy consumption and increased costs.
Fuel Type and Availability
The choice of fuel for your commercial boiler depends on factors such as cost, availability, environmental impact, and local regulations. Common fuel options include natural gas, oil, coal, biomass, and electricity. Consider the availability and cost of the chosen fuel type in your area to ensure a reliable and cost-effective supply for your boiler operations.
Efficiency and Energy Consumption
Efficiency is a crucial aspect of industrial boiler performance. Higher efficiency means more effective fuel utilisation, reduced energy waste, and lower operating costs. Look for boilers with high combustion efficiency and heat transfer capabilities to maximise energy savings. Energy-saving features such as condensing technology and heat recovery systems can further enhance efficiency and reduce environmental impact.
Emissions and Environmental Impact
Industrial boilers have a significant impact on air quality and the environment. Ensure compliance with local emissions regulations and consider environmentally friendly options, such as low NOx (nitrogen oxides) burners and emissions control systems. Investing in clean technologies not only helps protect the environment but also enhances the reputation of your business as a responsible and sustainable industry player.
Maintenance and Service Requirements
Proper maintenance and regular servicing are crucial for the smooth and reliable operation of industrial boilers. Consider the maintenance requirements, availability of spare parts, and the level of technical support provided by the manufacturer or supplier. A proactive maintenance approach helps prevent unexpected downtime, improves efficiency, and extends the lifespan of your boiler.
Installation and Maintenance of Industrial Boilers
Site Preparation and Boiler Installation
Proper site preparation and installation are essential to ensure the safe and efficient operation of industrial boilers. Engage qualified professionals to assess the site, determine the optimal location, and handle the installation process. Adequate space, ventilation, and accessibility should be considered to facilitate routine maintenance and inspections.
Start-Up and Commissioning Procedures
During the start-up and commissioning phase, it is important to follow manufacturer guidelines and industry best practices. This involves carefully calibrating control systems, conducting performance tests, and verifying the safety and operational integrity of the boiler. Thorough training of operators and maintenance personnel is crucial to ensure proper handling and troubleshooting.
Routine Maintenance and Inspections
Regular maintenance and inspections are vital to ensure the longevity and efficiency of industrial boilers. This includes tasks such as cleaning, lubrication, inspection of critical components, and testing of safety devices. Implement a proactive maintenance schedule and keep detailed records of maintenance activities to identify trends, plan repairs, and comply with regulatory requirements.
Troubleshooting Common Issues
Industrial boilers may encounter various issues during their operational lifespan. Understanding common problems such as uneven heat distribution, leaks, or combustion issues can help expedite troubleshooting and minimise downtime. Train your staff on troubleshooting procedures and have access to technical support from the manufacturer or experienced professionals.
Upgrades and Retrofits
To keep pace with evolving technologies and regulations, consider upgrades and retrofits for your industrial boiler. Upgrading control systems, improving insulation, implementing energy-saving measures, or integrating digital monitoring systems can enhance efficiency, reduce emissions, and optimise boiler performance. Evaluate the return on investment for upgrades and consult with experts to identify the most beneficial options for your specific requirements.
Safety Considerations for Industrial Boilers
Boiler Safety Standards and Regulations
Industrial boilers are subject to strict safety standards and regulations to protect personnel, equipment, and the environment. Familiarise yourself with relevant codes and regulations and ensure compliance with safety standards such as ASME (American Society of Mechanical Engineers) Boiler and Pressure Vessel Code. Regular inspections and certifications by authorised agencies are necessary to maintain safe boiler operations.
Pressure and Temperature Controls
Proper pressure and temperature control is vital to prevent boiler accidents and ensure safe operation. Reliable pressure relief valves, temperature sensors, and control systems are essential components that maintain optimal operating conditions within the boiler. Regular calibration and testing of these safety devices are necessary to ensure accurate and reliable performance.
Combustion and Fuel Safety
Combustion processes in industrial boilers involve potential risks, such as fuel explosions or combustion hazards. Implement robust safety measures, including flame detection systems, fuel shut-off valves, and proper ventilation, to mitigate these risks. Regular inspections, training of operators, and adherence to safety protocols are crucial to prevent accidents and protect personnel.
Water and Steam Safety
The safe operation of water and steam systems is paramount in industrial boilers. Adequate water treatment, including proper chemical dosing and monitoring, prevents scale formation, corrosion, and potential equipment damage. Ensure the availability of safety features such as low-water cut-off devices and steam pressure controls to safeguard against dangerous conditions.
Emergency Shutdown Procedures
Establish clear emergency shutdown procedures to respond swiftly to critical situations. Train personnel on emergency protocols, including shutdown sequences, isolation of fuel and power sources, and evacuation procedures. Regular drills and safety exercises can help familiarise employees with emergency response actions and ensure a swift and coordinated response in times of crisis.
Industrial Boiler Efficiency and Optimisation
Improving Boiler Efficiency
Efficiency optimisation is a key focus for industrial boiler operators to reduce energy consumption and operating costs. Implementing combustion optimisation techniques, such as proper air-fuel ratio control and burner tuning, can enhance efficiency and minimise emissions. Heat recovery systems, such as economisers and condensing technology, capture waste heat and increase overall system efficiency. Additionally, advanced boiler controls and automation enable precise control and optimisation of boiler operation.
Performance Monitoring and Optimisation
Continuous performance monitoring is essential to identify opportunities for optimisation and detect any deviations from expected boiler performance. Establish key performance indicators (KPIs) to assess parameters such as fuel consumption, steam production, and emissions. Regular performance evaluations, data analysis, and benchmarking against industry standards help identify areas for improvement and guide optimisation strategies. Implement continuous improvement initiatives to drive efficiency gains and ensure peak boiler performance.
Industrial Boiler Maintenance and Troubleshooting
Regular Inspection and Maintenance Tasks
Scheduled inspections and maintenance tasks are vital to ensure the long-term reliability and efficiency of industrial boilers. These tasks include boiler cleaning to remove scale and deposits, inspection and repair of insulation, and regular water treatment to prevent corrosion and fouling. Routine checks of safety devices, control systems, and fuel delivery systems are also essential to maintain optimal boiler operation.
Common Boiler Problems and Solutions
Industrial boilers may encounter common issues that can impact performance and reliability. Uneven heat distribution, which can lead to inefficient operation or equipment damage, can be addressed through proper burner adjustment or maintenance of heat exchangers. Boiler leaks and corrosion require prompt detection and repair to prevent further damage and maintain system integrity. Flame failure and combustion issues may stem from fuel supply problems, blockages, or improper airflow, which should be addressed through careful inspection and adjustments.
Emerging Trends in Industrial Boiler Technology
Digitalisation and Industry 4.0 Integration
The integration of digital technologies and Industry 4.0 principles is revolutionising the industrial boiler sector. Intelligent monitoring and control systems, remote operation and diagnostics, and predictive maintenance are becoming more prevalent. Real-time data analysis and machine learning algorithms enable proactive maintenance, optimised performance, and enhanced energy efficiency.
Energy Management and Sustainability Initiatives
Energy management and sustainability have become key priorities for industries across the globe. Industrial boilers play a crucial role in this pursuit, and several initiatives are driving the development of more sustainable and energy-efficient solutions. This includes the implementation of energy management systems, such as ISO 50001, which help organisations optimise energy usage and reduce their environmental footprint.
Advanced Combustion Technologies
Advancements in combustion technologies are continually improving the efficiency and environmental performance of industrial boilers. Innovations such as low-NOx burners, flue gas recirculation, and staged combustion techniques help minimise nitrogen oxide emissions. Furthermore, the integration of biomass and renewable energy sources as alternative fuels contributes to reducing greenhouse gas emissions and dependence on fossil fuels.
Remote Monitoring and Predictive Maintenance
Remote monitoring and predictive maintenance are transforming the way industrial boilers are operated and maintained. IoT (Internet of Things) technologies, sensor networks, and data analytics enable real-time monitoring of boiler performance, early fault detection, and predictive maintenance scheduling. This approach helps optimise maintenance activities, reduce downtime, and ensure the efficient operation of boilers.
Conclusion
Industrial boilers are the workhorses of various industries, providing essential heat and steam for manufacturing processes. Understanding the different types of boilers, their key components, and factors to consider during selection is vital for optimising performance and efficiency. Proper installation, regular maintenance, and adherence to safety protocols ensure safe and reliable boiler operations.
Efficiency optimisation, continuous performance monitoring, and the integration of emerging technologies contribute to enhancing the sustainability and environmental impact of industrial boilers. As industries continue to prioritise energy efficiency and sustainability, the evolution of industrial boiler technology will play a significant role in meeting these goals.
By staying abreast of the latest trends, embracing technological advancements, and implementing best practices, industries can harness the power of industrial boilers to drive productivity, reduce operational costs, and contribute to a greener future. As the industrial landscape evolves, industrial boilers will continue to evolve with it, revolutionising efficiency, performance, and sustainability in various industries.