Enhancing Laboratory Safety with Optimal Flooring: Our Project Overview
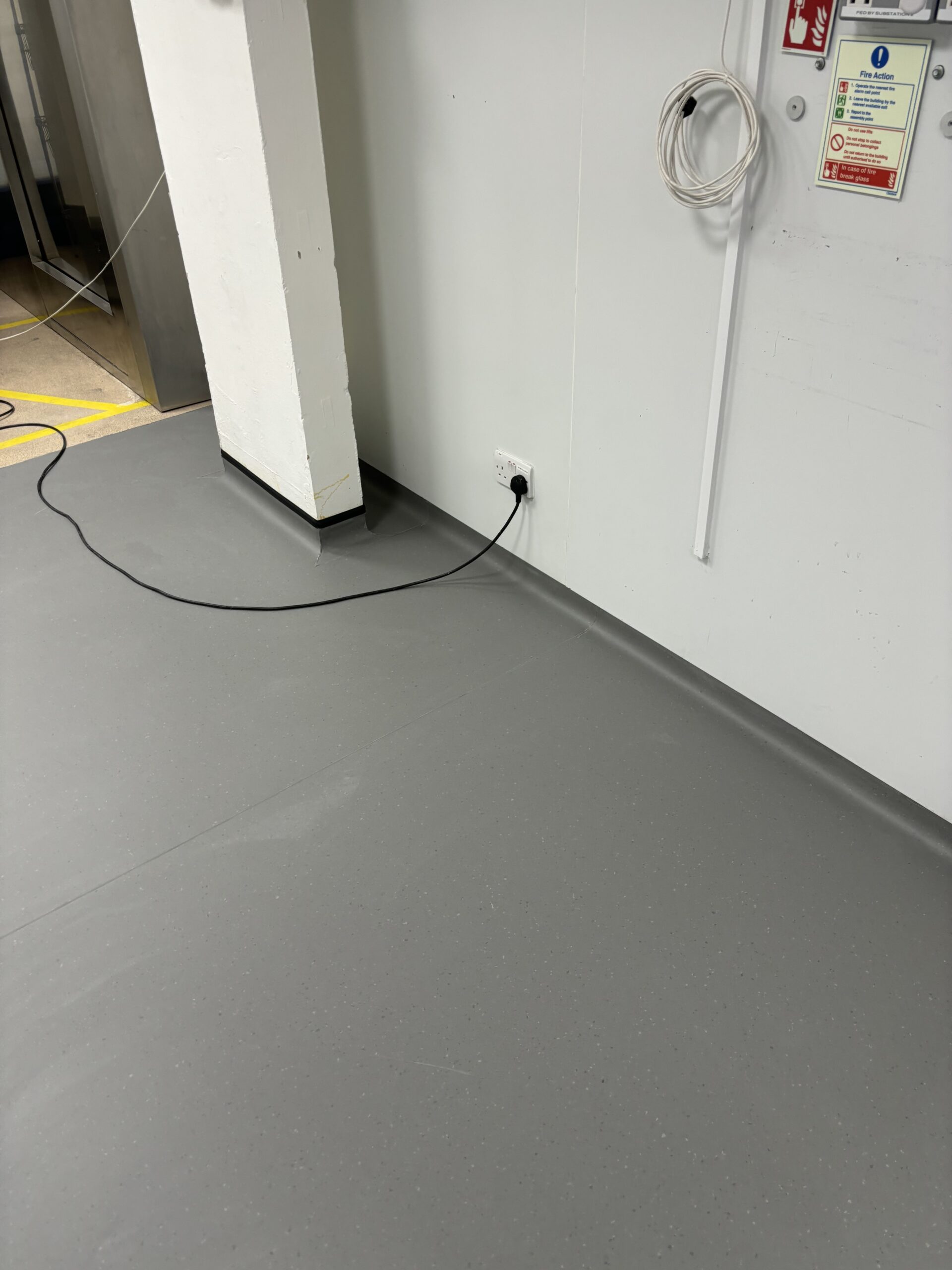
Enhancing Laboratory Safety with Optimal Flooring: Project Overview
We recently completed a flooring installation for a laboratory, focusing on creating a controlled, hygienic, and durable environment. This comprehensive guide outlines the key steps and considerations involved in the project.
Understanding the Requirements
We began by understanding the specific needs of our client, emphasizing a flooring solution that is:
- Slip-resistant
- Non-staining
- Non-permeable
- Moisture-proof
- Durable
- Easy to clean and maintain
Additional features required:
- Abrasion resistance for wheeled trolleys and forklifts
- Durability to withstand sharp tools or equipment drops
- Oil and grease resistance
- Hygienic, bacteriostatic, and anti-microbial properties
- Resistance to biocides
- Electrostatic-dissipative properties
- High and low-temperature tolerance
- Chemical resistance
Specifying Chemically Resistant Flooring
We analyzed the types and concentrations of chemicals the flooring would encounter, ensuring it could handle accidental spills and necessary clean-up protocols. We reviewed test data to select flooring that could resist specific chemicals and concentrations, providing long-term protection without frequent replacement.
Temperature & Cleaning Regimes
Considering the laboratory’s cleaning and sanitization methods, we chose flooring materials resistant to detergents, disinfectants, and high-pressure water. This ensured the flooring could withstand high-temperature cleaning processes, such as steam cleaning and hot water use, and resist decontamination chemicals like formaldehyde and fumigation agents.
Implementing the Solution
We recommended and installed seamless resin flooring to address common issues with sheet and tile products. Seamless resin floors offer a continuous surface without weak points, significantly reducing the risk of microbial growth and facilitating easier cleaning.
Integral Skirting
To further enhance hygiene, we extended the resin flooring up the walls, creating integral coved skirting up to 150mm high. This seamless finish prevents gaps where dirt or liquids could accumulate.
Ensuring Levelness & Flatness
We ensured the floors were smooth and level, with slight slopes towards drains to aid cleaning and decontamination. Slip-resistant drain covers were installed to enhance safety.
Electrostatic-Dissipative Properties
For environments requiring electrostatic control, we specified an anti-static resin floor system, ensuring electrical conductivity leakage resistance compliant with BS2050/1978 standards.
Special Considerations for PPE and Cleanliness
Given the laboratory’s stringent safety protocols, our team adhered to an extra level of personal protective equipment (PPE) requirements:
- Pre-entry showers and a complete change into disposable clothing
- Hair nets, snoods, footwear, and gloves
We operated with two teams: one inside handling the installation and a second team outside feeding in materials and consumables. Post-installation protocols included:
- Showers upon completion of work
- Use of Category 4 vacuum cleaners before wiping down and prior to client’s cleaning and fumigation
Waste materials were securely stored for six months before destruction to ensure complete safety and compliance.
Conclusion
Our seamless resin flooring installation provided a robust, hygienic, and durable solution tailored to the laboratory’s specific needs. By considering chemical resistance, cleaning regimes, and the need for a seamless finish, we ensured a safe and efficient working environment. This project demonstrates our commitment to quality and attention to detail, offering our clients flooring solutions that meet the highest standards of performance and safety.